GD & T / FEA
About Course
The GD&T / FEA Mechanical Course is designed to equip mechanical engineering students and professionals with in-depth knowledge of Geometric Dimensioning and Tolerancing (GD&T) and Finite Element Analysis (FEA). This course blends mechanical design theory with real-world analysis tools, enabling learners to interpret engineering drawings with precision and conduct stress, thermal, and dynamic analysis of mechanical components. By integrating design intent with analytical validation, this course builds a strong foundation for careers in product design, manufacturing, and simulation engineering.
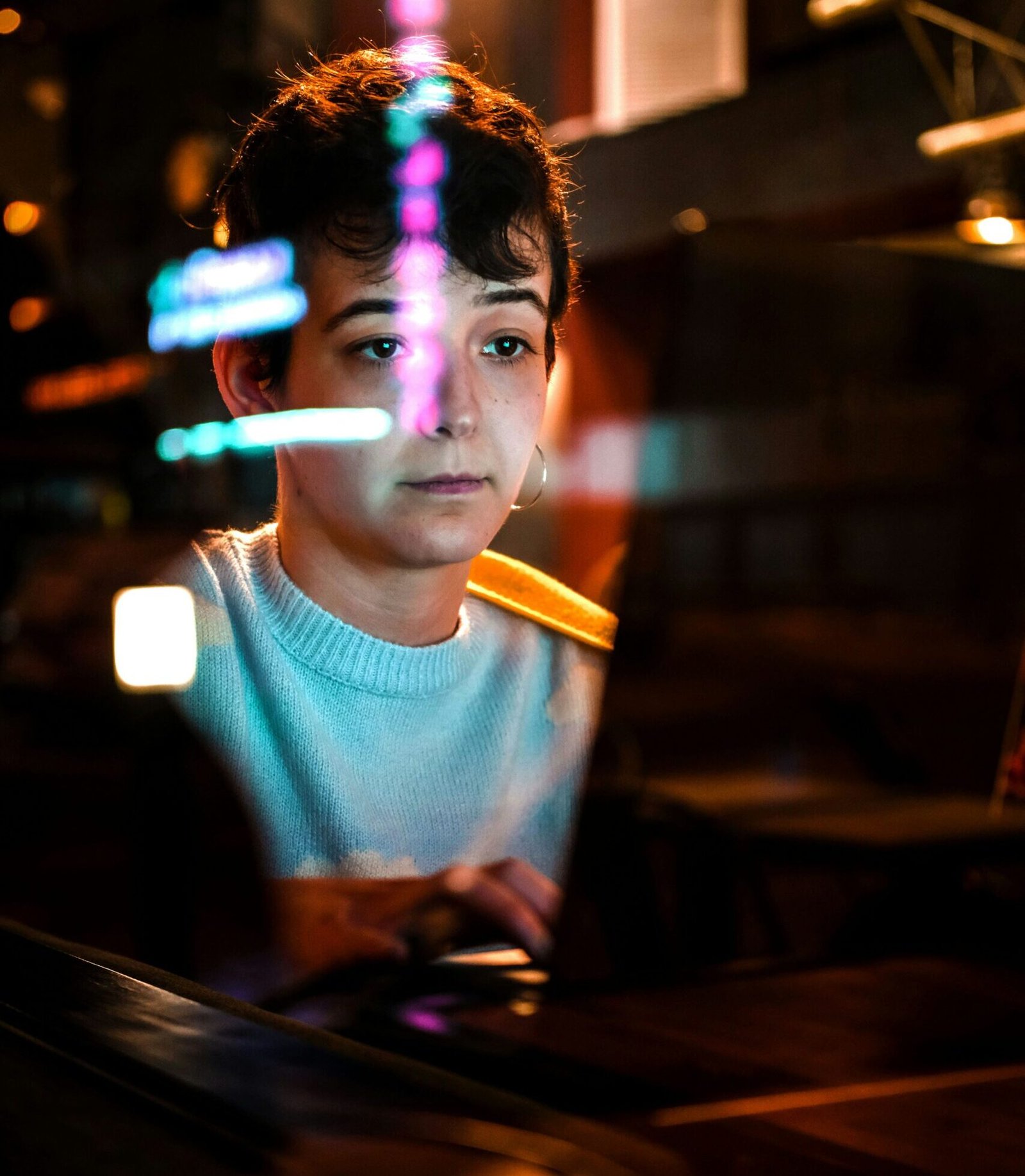
Course Objectives
Pre-requisties
The course is ideal for individuals with:
Basic understanding of mechanical engineering principles
Familiarity with CAD software (SolidWorks, NX, or similar)
Interest in product design, manufacturing, and analysis
Duration
Total Duration: 2 Months
▸ 1 Month of GD&T Theory and Application
▸ 1 Month of FEA Tools and Analysis ProjectsDaily Duration: 90 Minutes
Class Recordings: Available for self-paced revision
What You'll Learn
Fundamentals of Geometric Dimensioning & Tolerancing (GD&T)
Interpreting feature control frames, datum systems, and tolerance stacks
Design dimensioning best practices and tolerance optimization
Introduction to Finite Element Analysis (FEA)
Performing linear static, thermal, and vibration analysis
Material property selection and boundary condition setup
Validating product performance under real-world conditions
Using industry tools like ANSYS, SolidWorks Simulation, or equivalent
Who Can Join
B.E/B.Tech/Diploma students in Mechanical, Automobile, or Production Engineering
Working professionals in product design, quality, or simulation
CAD designers seeking to understand tolerances and product verification
Engineers preparing for careers in R&D, validation, or CAE domains
Training Curriculum
Introduction to Engineering Drawings and GD&T Symbols
Tolerance zones, MMC, LMC, RFS concepts
Datums and feature control frames
Application of tolerances in functional assemblies
Tolerance stack-up and design intent communication
Basics of meshing and model discretization
Stress, strain, and deformation theory
Static, thermal, and frequency analysis
Material selection and boundary condition setup
Result interpretation and design improvement
Dimensioning and tolerance assignment to a part/assembly
FEA analysis of real-world mechanical component
Final review of product analysis and optimization